
SAMPLE PROJECTS
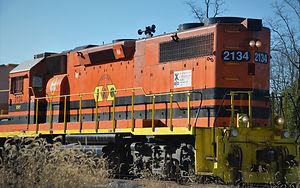
Railroad Performance Improvement
Contracted to reduce the dwell time for one shop of a large class I railroad in North America. Trained teams of managers, supervisors and operators in lean tools and techniques and led the implementation. Improved 5S of the shop, improved visual management, created standard work job instruction sheets, trained supervisors and managers in leader standard work using management kamishibai (management K-cards), and improved locomotive inspection and flow through the shop. This resulted in saving several million dollars per year in one shop alone. The program was then transferred to all other shops across the network, in conjunction with a newly developed continuous improvement department. The CI managers and practitioners were trained as we rolled out the process to the new locations.

Carpet and Commercial Flooring Improvement
Contracted to improve the Overall Equipment Effectiveness (OEE) of 4 plants for a large carpet manufacturer. Designed and implemented a 10 week improvement plan for each facility. The plans consisted of; improving TPM, Changeover reduction, standardized work, 5S, Kaizen workshops, improved visual management and Leader Standard Work (Management K-cards). Each plant realized OEE improvements in the 15 to 30% range for several million dollars in total savings. In addition, this work led to the creation of a dedicated continuous improvement department within the organization.

Private Equity Portfolio Company - Candle Manufacturing
Shortly after PE acquisition of a large candle factory in the midwest, the leadership team realized that there were deficiencies and gaps in the operation that needed to be addressed. I was brought in to work with the local management team to design and execute a 6 month recovery plan. This focused on leveling up the skills of the plant leadership and key hourly employees while establishing foundational tools and standardized work plans on the shop floor.
Visual management, standard work, centerline creation, visual KPI’s and Management Kamishibai (leader standard work) all had a positive impact on improving throughput, yield and reducing downtime. Focus on right sizing the temporary to permanent labor helped to solidify the foundation of the improvements. Shop floor kaizen events created excitement and engagement of the workforce, as well as identifying over $1.7 million in savings.
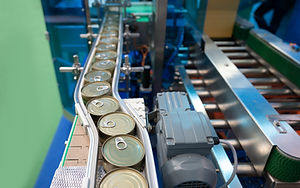
Private Equity Portfolio Company - Pail and Can Manufacturing
Engaged to assist a PE portfolio company with improving their scheduling process. From customer order to delivery, there were many delays and breaks in the existing system. Using a cross functional team composed of; scheduling, accounting, supply chain, customer service, sales and manufacturing personnel, the team was led through a one week order to delivery brown paper exercise. During the week, the team mapped out the process and focused on identifying potential issues and breaks with the current process. They also created business rules for pail assembly, developed and optimized production schedules, standardized processes, and started investigation into product standardization (reduction of SKU’s). The team also turned this into a model that was then successfully expanded to other areas of the business over the next few months, resulting in a robust highly functioning scheduling process that was firmly integrated into the business.